What is Dynamic Balancing in Industrial Applications?
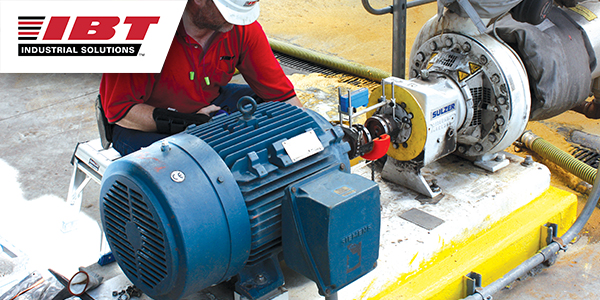
Dynamic balancing is the process of running a piece of equipment at a given speed, measuring the dynamic imbalance, and correcting via the addition or removal of weight. This can be achieved by sending the rotating assembly out to a specialized shop or making the appropriate corrections on-site using field balancing techniques.
Field balancing provides high-quality balance grades with minimal downtime when compared to shop balancing. Another advantage of dynamic field balancing is that the equipment is balanced in place at your specified running speed. Oftentimes, the balance grade achieved with a shop balance can be diminished when the rotating assembly is reinstalled.
Correcting imbalance involves measuring the amplitude of the vibration signal produced by the imbalance and determining the phase (or location of the “heavy spot”) relative to a reference signal. Dynamic balancing is most often performed on industrial fans, hammer mills, and rotating equipment that is too large to remove and place in a conventional balance stand.
Excessive imbalance of rotating equipment can lead to serious mechanical failures and result in unexpected and costly downtime. For these reasons, detecting potential causes early on can be crucial for your operation. In this article, IBT’s Industrial Maintenance Technologies Group (IMT) shares some common factors that require dynamic balancing.
Common Factors that Require Dynamic Balancing
The earlier the imbalance is detected, the less damage will occur, and the more likely it is that you’ll be able to save on repair costs. When rotating equipment is properly balanced, you’ll see consistent and smooth operation, increased bearing life, and less dynamic load on the components and structures.
That’s why it’s important to keep certain factors in mind when it comes to performing dynamic balancing on your equipment. Here is a list of some of the most common instances for addressing imbalance:
1. When there is significant material buildup present, operating conditions can cause wet or sticky matter to adhere to the surfaces of the rotating machinery and can cause significant imbalance. The best practice is to clean the rotor of all product/material buildup; however, this is often impractical or next to impossible.
We are sharing this content on behalf of IBT Industrial Solutions, a GEAPS Premier Partner. If your company is interested in opportunities such as this, please reach out.