Mr. Voigt is president of JFV Solutions. He formerly worked at ADM, where he was vice president of operations and engineering for the domestic and international grain divisions. His responsibilities included operational and engineering activities for all origination, terminal, and port grain handling facilities located in North, South, and Central America. Jim also co-founded the Operational Continuous Improvement Team within ADM. He is a past International president of GEAPS.
Management Basics for Grain Facility Supervisors
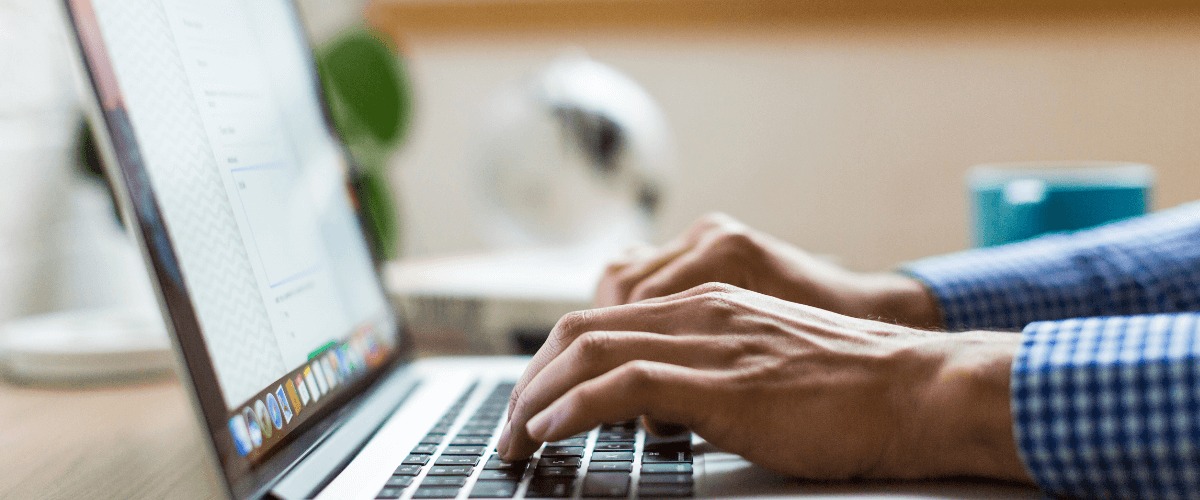
GEAPS Online Learning courses are available anytime on-demand. Each course takes approximately 10 hours to complete and can be completed at any pace over five weeks. Courses must be completed within a five-week period that begins the day you register. After registering, learners will be sent a confirmation email, then you’re ready to start learning!
Cost:
$495 for members
$795 for non-members.
Course Description: Managing and supervising grain facilities are increasingly complex jobs, entailing many diverse responsibilities and a lot of knowledge. This course outlines and examines the main duties, ranging from budgeting, accounting and insurance to maintenance, safety, regulatory compliance and effectively managing employees.
Course Goals: This course will provide an extensive overview of the main duties, responsibilities and expectations of grain operations supervisors and managers. It will indicate what duties, topics and roles supervisors and managers need to understand — and why they need to understand them. The course will also provide companies with a basic training tool for new and prospective grain-facility managers and a refresher for people already in management positions.
Target Audience: New or prospective managers or supervisors of grain facilities; people to be promoted into supervisory or facility manager roles; companies that need to train new supervisors and managers; new owners of grain facilities; people who may want to pursue managerial or supervisory roles in grain operations; current managers interested in learning more.
Instructors:
Dr. Jonathan Shaver is the founder and owner of Envision Partners. He prepares and supports new and experienced technical managers to lead teams, motivate employees and provide effective communication. Jonathan worked in the food and agriculture industry for 15 years, including for Monsanto and Oklahoma State University (where he was the Crops Judging coach), before starting his own business. He has experience in the government regulation of genetically modified plants and in animal testing.
Sara Kepley joined ProValue, LLC in 2007. Prior to joining ProValue she worked for Human Resource Alliance, LLC as a shared service human resource consultant for a group of fourteen agriculturally focused companies in South Central and South Eastern Kansas. Sara has a bachelor’s degree in human resource development from Southwestern College and is currently pursuing her MBA at Wichita State University. In 2006, she earned her Senior Professional Human Resources designation.
Jay O’Neil has 40 years of trading and management experience in the grain industry. He has worked for Continental Grain Company, the Pillsbury Company, the Ferruzzi Group and Bartlett Grain Company. For the past eight years, he has operated his own private consulting company. Jay publishes a private weekly ocean freight and transportation report. He is currently employed as the senior agricultural economist for the International Grains Program at Kansas State University. He served for many years on the National Grain & Feed Association Trade Rules Committee. He is also a past chairman of the North American Export Grain Association Contracts and Arbitration Committee and is an emeritus member of this committee. Jay continues to serve as an arbitrator with both associations. He graduated from San Jose State University in 1973 with a degree in political science-international relations.
Al Tweeten has 30 years of property and casualty loss control experience, including 15 years of commercial agribusiness loss control experience. He has worked as a regional safety specialist for GROWMARK, a loss control consultant and supervisor for MSI Insurance, and most recently for Berkley Agribusiness Risk Specialists as VP of risk control. He earned his Bachelor of Science in occupational safety from Iowa State University. Al has also obtained his CPCU, ARM, ALCM insurance designations.
Brandon currently works at American Central Transport, inc. (ACT) where he serves as the Director of Risk Management. Prior to ACT, Brandon has held positions with Honeywell, The Scoular Company and Nationwide Agribusiness Insurance in roles that focused primarily on risk management and safety. Brandon has continued his professional education by obtaining various certifications from OSHA and other trade organizations within the grain handling industry. He has received his Associate Safety Professional (ASP) designation from the Board of Certified Safety Professionals and he is actively working towards his Certified Safety Professional designation. Brandon is also involved with GEAPS, serving as a past president and board member for the Kansas City Chapter. He has also served as an officer within the Kansas City chapter of the American Society of Safety Engineers (ASSE) organization. Brandon is a 2006 graduate of the University of Central Missouri, where he earned his Bachelor of Science in Safety Management.
Randy Springer became interested in safety and maintenance programs when he spent 11 years working as a grain elevator superintendent after college. In 1997, he co-founded Pepper Maintenance and in 2008, he, along with his wife, became the sole owner. Pepper Maintenance began with a specialization in infrared and vibration technologies, but has expanded to include precision laser installation and alignment, ultrasonics, thickness testing and LDAR. Pepper currently serves companies in 44 states and Canada, which has led to its recognition as a leader in the field of preventive maintenance. As President and CEO of Pepper Maintenance, Randy is certified as a Level 3 Thermographer, holds several vibration certificates, and has many years of experience in laser alignment and ultrasonics. Randy graduated from Goshen College.
The Course of Study
Lecture 1 – Policies and Procedures
This lecture will discuss the basic responsibility of grain facility supervisors and managers to learn what their corporate and site-specific policies and procedures are, how to follow them — and where to find them. Managers need to know what site-specific policies are required that may not be covered by the corporate office. What are all the policies that supervisors need to manage… Whether there is an organizational chart showing who is in charge of a facility’s functions and duties… Who is on the manager’s support team… Where to go for information, guidance, help and authority with employment, safety, payroll, procurement, accounting, worker’s comp and other issues. The lecture will also point out the need to learn about employee handbooks. Does your company or facility have one? What does it cover and what doesn’t it cover? What doesn’t it cover at your facility?
Lecturer: Jon Shaver
Lecture 2 – Safety Management
Facility managers need to know the scope of their safety responsibilities, how to fit into the corporate safety structure, and how to allocate sufficient time and resources to get the job done right. This lecture will discuss the importance of understanding the facility security and emergency action plans, the loss prevention plan, and the hazard communication plan. It will also point out the purposes of safety handbooks; discuss key issues in dealing with employee and contractor safety, and what kinds of safety training to provide to new employees. It will also consider approaches for handling public relations in an emergency.
Lecturer: Brandon Leininger
Lecture 3 – Basic Accounting for Grain Facility Supervisors
This lecture will point out the importance of the interaction between accounting and the successful operation and management of a grain handling facility. The viability of a business is based on the accuracy and timeliness of the data and reports used in decision making and management of the assets. This lecture will look at the collection of raw accounting data from various sources within the operation of the facility and its conversion into meaningful reports.
Lecturer: Jim Voigt
Lecture 4 – Budget Management
This lecture will point out the need for developing an annual operating budget, where to find out what expenses were, what taxes were, why managers need to know what expenses are in detail, what labor costs vary periodically, etc. — buy a bucket elevator, capacities, 100 examples… a good starting point on how to start up a budget…
Lecturer: Jim Voigt
Lecture 5 – Inventory Management
Grain facility managers need to understand what their roles are for managing inventory. This lecture will discuss what managers need to keep track of and why. It will point out value of tracking shrink, preventing theft and fraud, drying and mixing issues, aeration, fumigation, temperature-monitoring, moisture-testing, grading, sampling and other considerations relating to inventory.
Lecturer: Jim Voigt
Lecture 6 – Capital Project Management
What are your company’s policies regarding capital projects and spending for capital projects? What is the protocol to get capital projects approved? Who should manage each project and why? How do you go about developing a capital plan, or calculate return on investment? What are your financial restrictions, and what do they apply to? How do you ensure that you get precisely what you paid for? What do you need to provide to contractors so that they do exactly what you need? What is the importance of getting competitive bids? How can you procure materials?
Lecturer: Jim Voigt
Lecture 7 – Human Resources, Employee Management
This lecture will help students understand their basic responsibilities as managers of people. What you need to do for your employees to ensure that they work efficiently? What is your employee-orientation policy? Why are job descriptions and performance evaluations needed? What is the performance evaluation process? How should your employees be held accountable? What are the policies that should be used to hold them accountable? What are the corporate or site-specific work standards? What are the standard operating procedures for various job functions? What are the customer-service expectations? What is the attendance policy?
Lecturer: Sara Kepley
Lecture 8 – Marketing and Transportation
Who does what and how is it done at your facility? What is the cost of handling? This lecture will provide a basic understanding of manager’s role in grain marketing, and how it affects his job duties. What are the transportation choices at your facility? Why you need to know your shippers and their rates and costs, about demurrage, and how to make good decisions on shipping options?
Lecturer: Jay O’Neil
Lecture 9 – Insurance Management
What are a grain facility manager’s main roles in managing insurance? What are the different types a supervisor may have to manage? (Property, liability, health, worker’s comp, etc.) What do insurance carriers expect from a facility manager? What is the claims process? What are a facility’s limits in each category before you to claim? When do you claim? When don’t you claim? What is an insurance audit? Legal implications to what may happen if you do not have specific types of insurance…
Lecturer: Al Tweeten
Lecture 10 – Maintenance Management: The Key to Our Success
What are a manager’s main roles in developing and maintaining a maintenance program? What’s needed in a maintenance program and why have one at all? What are recordkeeping requirements of a manager? Importance of knowing emergency maintenance contacts when something breaks down during harvest? What parts do you need to keep in stock? What parts can you easily source elsewhere? When can you rely on in-house maintenance and when do you have to go elsewhere for services?
Lecturer: Randy Springer
Lecture 11 – Regulatory Compliance
What are main roles of managers and supervisors? How can they keep up with regulatory changes, stay in compliance? What are the paper requirements and time commitments? What kinds of permits are needed at the facility? Where should you keep permits on site? How do you deal with state grain inspection licenses and auditors? Scale tests, moisture meter tests? What has to be tested and how often?
Lecturer: Jonathan Shaver