Before arriving at KSU in 1994, Fred Fairchild had more than 30 years of industry experience in the design, construction, operation and management of feed, flour, dry corn milling and pet food manufacturing facilities. A professor of grain science and industry, Fairchild worked previously at Todd & Sargent in Ames, Iowa, where he was vice president of engineering. A licensed professional engineer, Fairchild specializes in plant design and construction, manufacturing technology, maintenance, materials handling and plant management.
Grain Facilities Planning and Design II
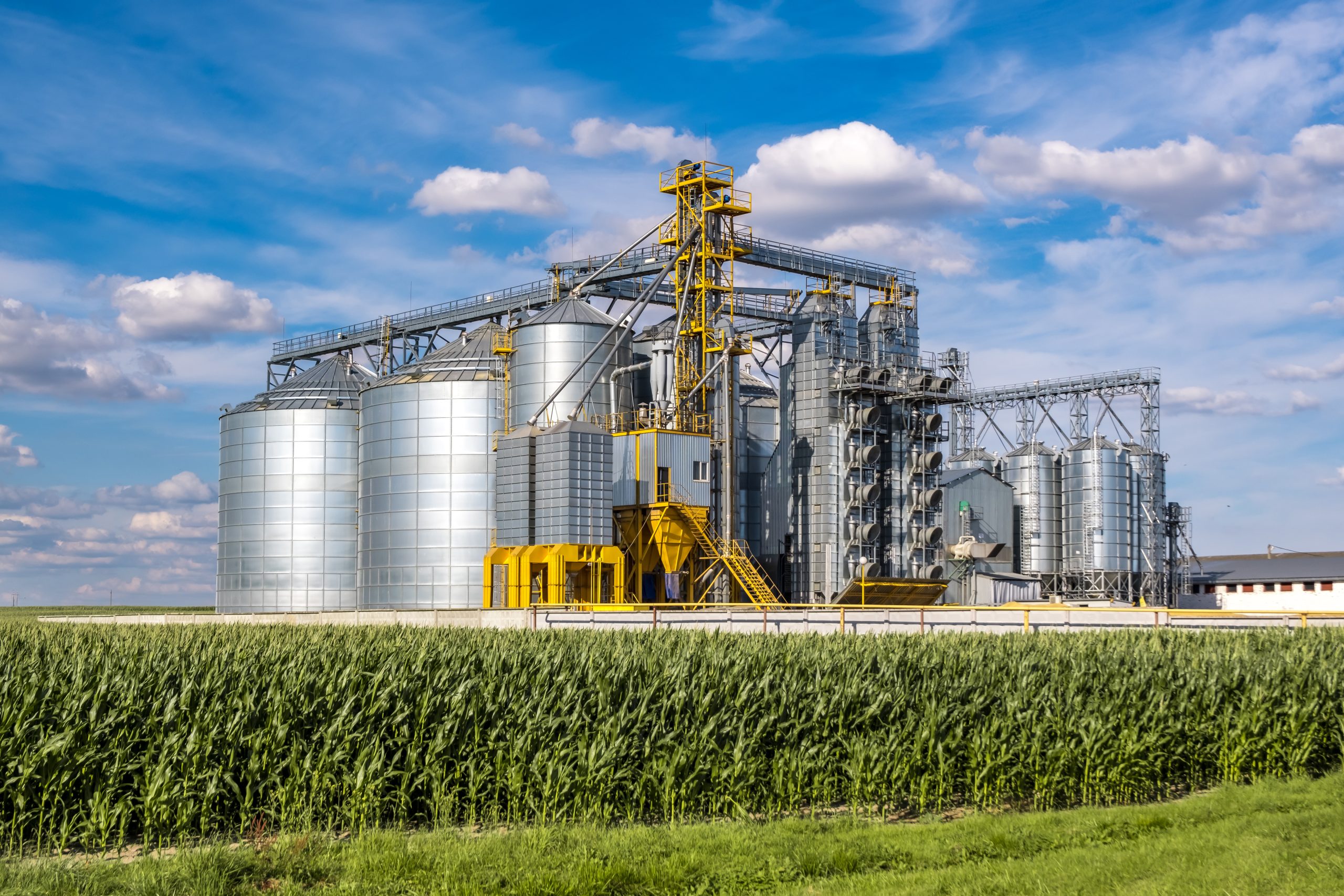
GEAPS Online Learning courses are available anytime on-demand. Each course takes approximately 10 hours to complete and can be completed at any pace over five weeks. Courses must be completed within a five-week period that begins the day you register. After registering, learners will be sent a confirmation email, then you’re ready to start learning!
Cost:
$495 for members
$795 for non-members.
Course Description: Facilities and Planning Design II is the second of two courses developed to help grain industry professionals understand key issues relating to planning and designing grain facilities. The course goes beyond the basics, and is intended for people with some experience dealing with grain facility planning and design considerations, or who have completed Facilities Planning and Design I.
Course Goals: This course is designed to provide a practical, real-world foundation for grain industry operations professionals responsible for helping plan and design grain facilities. It will enable improved input into decision-making across a wide range of plan-design considerations, including facility siting, rail and track layout, automation and control systems, safety and security, plumbing and lighting, temporary storage, roofing and waterproofing and improvement/expansion projects.
Target Audience: This course is intended for grain operations professionals with decision-making duties relating to how grain facilities and their internal systems and layouts are planned and designed. The course is recommended for those who have completed Facilities and Planning Design I or have equivalent experience, and is not for beginners. Specifically, it is designed for operational management — people with a professional need to provide input into planning and designing a new grain facility, or expanding or retrofitting an existing facility.
Over ten years ago, Mike Eldridge joined his father’s business, Ameritrack Railroad Contractors, which is now called Ameritrack Rail. Over the years, his knowledge, experience and AutoCAD skills helped expand the company’s business from small regional engineering projects to larger engineering projects across the Midwest. Eldridge has designed over 50 industrial rail projects, including Class I railroads and shortlines throughout the U.S. Although the majority of his work is in the grain industry, he has also managed projects in the ethanol, steel and chemical industries.
Colin Martin has worked for Stockdales Electric Motor Corp. in Regina, Canada, since 2002, with a major focus on grain/agricultural facilities. He currently leads a team of engineers and technologists to serve Stockdales’ customers in both Canada and the U.S., and has automated projects ranging from small seed cleaning plants to the largest inland grain terminals in Canada. His professional experience includes electrical design, safety and detection devices, software design, integration with ERP systems, on-site commissioning and support. Martin graduated from the University of Regina with a bachelor’s degree in computer science and also has an electrical engineering technologist’s diploma from SIAST Moose Jaw.
Peter Walker recently retired from Parrish & Heimbecker Ltd (P&H), where he worked with safety programs throughout the Canadian grain industry. He was the safety manager for six years, responsible for developing, implementing and auditing the safety program for 18 grain elevators in Western Canada. Prior to P&H, he was the plant manager at Molson Breweries and the Parmalat Dairies, both in Winnipeg. Walker earned his bachelor’s degree and Master of Science in Microbiology.
Greg Thirnbeck is senior vice president of Contract Administration at D.C. Taylor Co., a company that specializes in industrial and commercial roofing. In this role, he works with members of the food and grain processing industries across the nation. He aids the company’s processes for insurance and risk management, and handles negotiations for their contract terms and conditions. Thirnbeck is a registered Roof Consultant and is currently a member of RCI, Inc. (formerly the Roof Consultants Institute), the National Roofing Contractors Association and the National Roofing Legal Resource Center. Thirnbeck is also a RoofPoint Registered Professional through the Center for Environmental Innovation in Roofing.
Josh Spegel joined Michigan Agricultural Commodities as a safety and security manager in 2012. Spegel helps oversee and regulate all aspects of security and safety; including technology, equipment, procedures and theft detection. Spegel and his team continuously conduct self-audits to improve performances and practices. Before working at his current company, Spegel worked for nine years at Dow Chemical Co., the largest chemical facility in Michigan.
Bob Marlow is a consultant and training specialist providing technical and managerial training for all phases of grain facility operations, including grain quality management, facility efficiencies and maintenance/project management. Bob is a lecturer and instructor with GEAPS and Kansas State University in their Hands-On Training (HOT) Program and Grain Elevator Manager (GEM) course. He has also collaborated with and is an instructor at Iowa State University on their Advanced Grain Elevator Manager Course. Following Dr. Carl Reed’s retirement, Bob continues to use both Carl’s and his own materials that cover the broad managerial and technical skills required in today’s challenging grain facility operations.
Bob Klare is an experienced and insightful consulting engineer, passionate about developing bulk handling facility concepts and arrangements that enable clients’ business models to succeed. With twenty-five years of experience in design, construction, maintenance and operations of some of the world’s largest bulk handling facilities, Bob incorporates proven technologies and innovative arrangements to maximize operational capacity and flexibility, while controlling capital, construction and operating costs.
The Course of Study
Lecture 1: Site Requirements
Lecture 1 will take an in-depth look at site selection. It will address soil sampling, foundations, drainage and engineering controls; areas needed to effectively locate scales, dump sites, probes, and other systems or equipment; allowing enough space for effective traffic flow; public access and access for the handicapped; office-space, laboratory and recordkeeping needs; and site-selection and design issues that pertain to getting along with neighbors.
Lecturer: Fred Fairchild
Lecture 2: Rail Planning and Track Layout
This lecture will investigate how to plan and design for effective rail service into and around a grain facility, calculate the areas and dimensions needed to accommodate rail access, and discuss optimal track layout and coordinating plans with the railroads. The lecture will emphasize the need to ensure that designs match internal circumstances relating to switching capacity, car-handling equipment, and the type of locomotives in use or that would be required for expanded handling capacity.
Lecturer: Mike Eldridge
Lecture 3: Selection and Application of Sensing Units
Lecture 3 is the first of two lectures about sensors, and how they influence facility design. It will discuss various sensor types used in grain facilities, what types of signals they emit, how to coordinate sensor use, where the sensors should be mounted, and safety and insurance requirements and considerations.
Lecturer: Colin Martin
Lecture 4: How to Use and Manage Sensor Information
Continuing the discussion, Lecture 4 will cover two main topics. Part 1 will address designing for the relationship between sensor location, computer automation systems, and follow-up. In what parts of a grain facility should alarms sound? Will someone be needed to respond in all cases, without fail? How is the sensor and alarm information stored? When a signal goes off, what is the process for addressing the cause and appropriately tracking the information? Part 2 will discuss how to plan and design for facility automation and controls in a retrofit. How do you integrate the existing equipment?
Lecturer: Colin Martin
Lecture 5: Designing for Safety
This lecture will discuss safety considerations when planning a new facility or expanding or upgrading an older one. What’s the best way to plan for reducing hazards, complying with the rules and regulations, access control, equipment guarding, catwalks, manholes, trip-lines, stop cords and explosion venting and suppression.
Lecturer: Peter Walker
Lecture 6: Designing for Security
Security at grain facilities has become increasingly important in recent years, and effective design can go a long way toward keeping intruders at bay. However, it’s also important to recognize early in the design process that a cookie-cutter approach to security will not work. Grain facilities differ too greatly in type, style, layout, size, location and points of access, and most (including yours) will have unique security needs. This lecture will help grain-facility planners and designers identify key security considerations, and prompt essential questions about gates, perimeter fencing, theft-detection, video surveillance and other security requirements and options.
Lecturer: Josh Spegel
Lecture 7: Planning for Retrofit and Expansion
If you’re adding to an existing facility or upgrading equipment, it’s advisable to take a good hard look at just about everything. This lecture will discuss primary considerations when planning for an equipment retrofit or an expansion. How much additional capacity will be needed in the various facility systems? What sizes of motors will be required to move additional volumes of grain? What would be the most efficient motors for your retrofit or expansion? What types and capacities of conveyance equipment? How much additional space will you need, and where will you need it? What type of interfaces and connections are needed between the old and new? How do you ensure that existing and new equipment is compatible and can handle expanded capacities and speeds?
Lecturer: Fred Fairchild
Lecture 8: Roofing Design, Waterproofing and Coatings
The selection and installation of an appropriate roof system is critical for grain protection and worker safety. Grain operations professionals will need to consider a range of factors that are unique to their situation and needs during the planning process. This lecture will discuss a variety of roofing materials, their purpose and characteristics, and the challenges and benefits of using them. Students will evaluate roof decks in terms of their suitability as a substrate and roof membranes in terms of their resistance to weather, durability and serviceability. Project planning and execution will also be covered, including selecting contractors and identifying potential access and loading obstacles.
Lecturer: Greg Thirnbeck
Lecture 9: Temporary Storage
Numerous types of temporary storage systems have been devised over the past several years, and many grain companies are making them essential parts of the storage strategies the company may be using. This lecture will discuss how to select the best type and construction for a specific location and needs.
Lecturer: Bob Marlow
Lecture 10: Utilities
This lecture will investigate options for utilities systems in grain facilities, and how they need to be taken into full consideration in the planning stages of a green-field or expansion project. Topics will include electrical service, water and plumbing, fuel sources for heating and drying, compressed air and related matters. What are the costs?
Lecturer: Bob Klare